Microscale Fastening System in
Mechanical Watches
MIT Culpepper Lab, Oct. 2022 - Sept. 2023
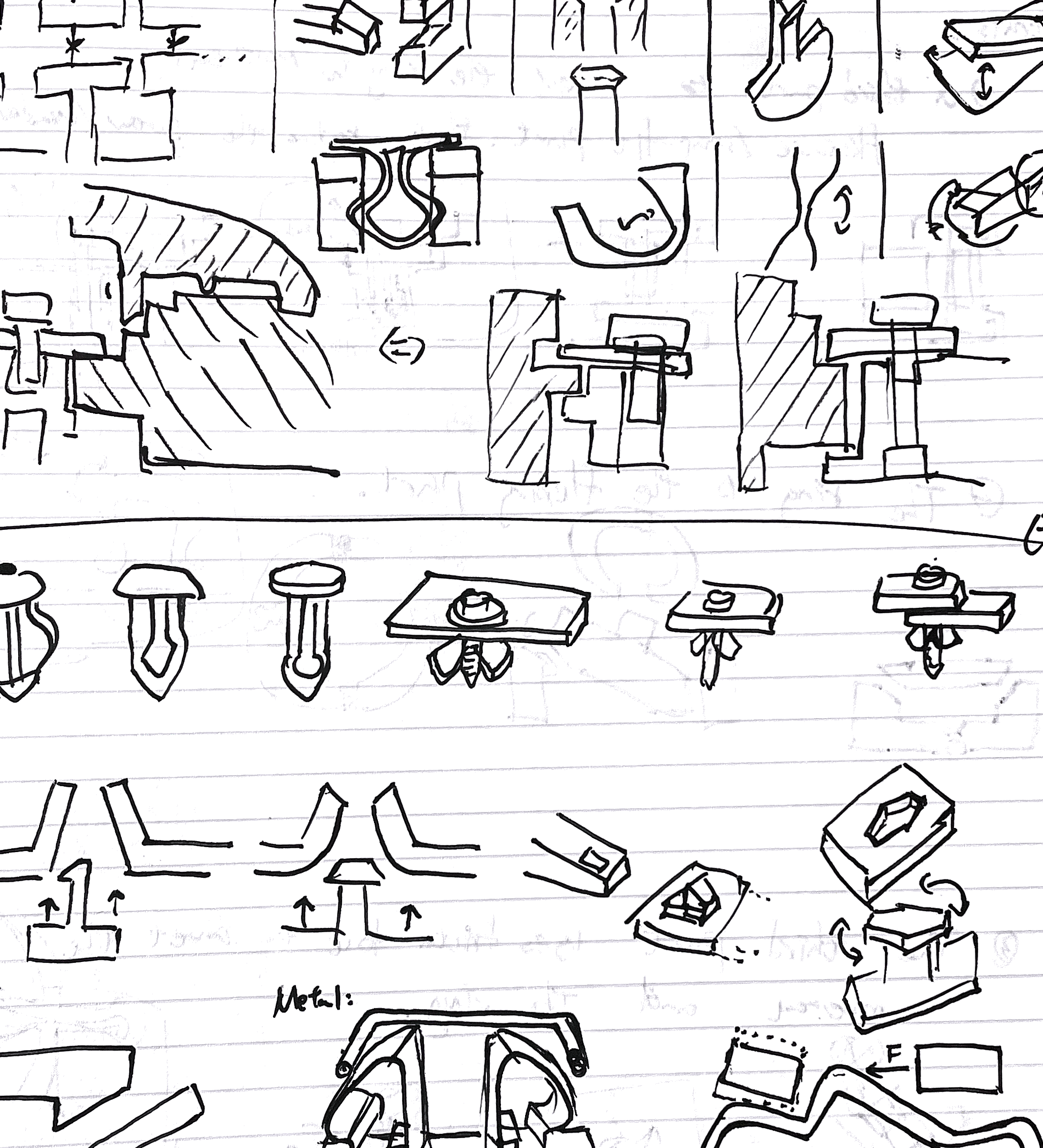
Research Project
ProductDesign/Mechanism
In this long-term project, we are developing a new microscale fastening system for mechanical watches. Constrained by size, material, and precision requirements in watch design, the goal is increasing shock absorption and reducing failure rates to improve durability, while also considering manufacturability and ease of assembly. Due to confidentiality, some pictures and results are omitted here.
Skills
- SolidWorks/FEA
- Manufacturing
- Precision Design
- Patent Development
Supervisors
- Prof. Martin Culpepper
- Alejandro Martinez
- Luke Hardy
Material Testing / Selection
The small scale of watch mechanisms constrains the materials we can use. A series of tests were performed to help us understand material properties at this scale.
Design Simulation / Prototypes
Through a series of design iterations, we downselected several possible mechanisms to investigate. We created larger-scale models and simulations for each of these to see if they were functional when applied to the smaller scale. We used standard methods, including FEA, Matlab simulations, and building prototypes.
Fatigue Testing / Impact Testing
After designing the mechanisms, we simulated their performance under different loads and employed drop tests, shock tests, and vibration tests. We used the results from our tests to iteratively improve our microscale designs.